top of page
3D Weaving Technology
Composites
Composites materials are traditionally produced in two dimensions by placing layers of material on top of one another over a mould and infusing them with the resin. This creates a 3D laminate and relies solely on resin to bond each layer together.
This method is prone to inter-laminar shear stress which causes the layers of the composite to separate under stress loading, and is known as delamination. This is an inevitable consequence of traditional 2D weaving technology.
The OPTIMA 3D weaving system overcomes this problem by weaving a strengthening fibre in three dimensions, to a pattern determined by the component design.

3D Weaving
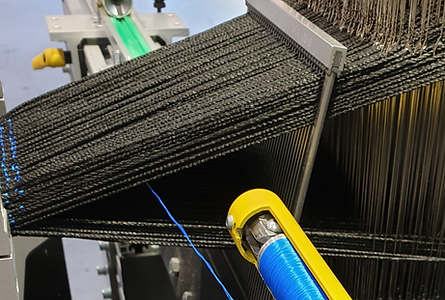
A primary benefit that can be gained by 3D weaving is increased structural integrity due to the reinforced woven shape.
The utilisation of a loom to weave interlocked Warp and Weft yarns between layers and through the thickness of the fabric, with further continuous interlocking of Weft yarns via Shuttle.
This results in a 3D composite material that is better able to cope with impacts, or loads such as bending, without delamination.
Research has indicated that such processes can produce materials that exhibit fracture toughness up to 20 times higher than conventional laminates.
Quality Assurance Benefits
An equally key benefit of the OPTIMA 3D weaving system is the quality assurance and repeatability that our fully automated process confers on the engineered solutions; a level of benefit which is simply not achievable with lay-up techniques.
This is vitally important for accreditation of the manufacturing process and subsequent approval processes that are increasingly vital for industry.
These attributes are significantly important in key areas such as aeronautical and defence engineering, however emergence of 3D technology into the mainstream of engineered component production will inevitably reduce manufacturing costs whilst at the same time decreasing delivery times; this will lead to much wider use in more general industries.

bottom of page